M.Sc. Kevin Hansch
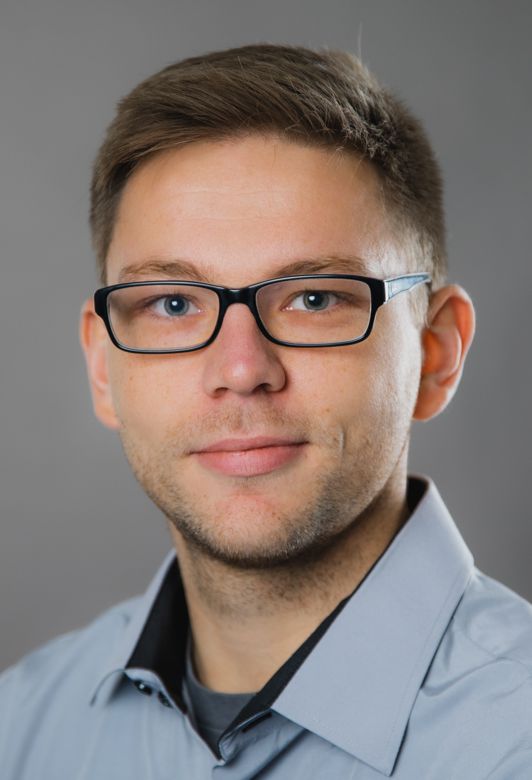
M.Sc. Kevin Hansch
Production Systems and Automation (IEPS)
Kevin Hansch studied mechanical engineering at Otto von Guericke University Magdeburg, specialising in production engineering, and completed his master's degree in December 2018. After working as a project manager at BOHAI TRIMET Automotive Holding GmbH, he has been working as a research assistant at the IAF since December 2022.
Current projects
Digital plant modeling with neutral data formats (DIAMOND) Subproject: Consistent, process-oriented data models in the engineering of production systems (KPDM)
Duration: 01.11.2022 to 31.10.2025
When new products are introduced, existing production systems have to be expanded or modified. New manufacturing processes are derived from new products, which are implemented either manually or using plant technology. This system technology (resources) is therefore directly linked to changes to the product and process. The plant life cycle contains a large number of individual data-processing processes in various engineering disciplines, many of which are design processes. Each of these disciplines already works with digital models. The individual steps build on each other and each discipline consumes information from the previous process. Currently, this information is usually transferred manually, which takes a lot of time and leads to an increased number of errors. This also applies to the entire ecosystem, in which component manufacturers, for example, extract the relevant information from their own engineering and make it available to the entire value chain. However, the current speed of transformation in the automotive industry no longer allows for long project runtimes and negative quality influences. It is therefore necessary to make changes available to all those involved in the process in a timely manner and to enable a common "picture" via an efficient exchange of information. The main objective of the OvGU within the DIAMOND-KPDM project is the development and application demonstration of a procedure for the application-specific creation and use of a system of coordinated domain-specific and cross-domain data models, the so-called Common Data Model, which enables an efficient and effective design of production systems through an efficient and effective transformation, integration and selection of design data.
This text was translated with DeepL
Completed projects
Workflow automation in order processing (ATAautoWorkflow)
Duration: 01.04.2024 to 31.03.2025
The aim of the project is to identify possibilities for the systematic automation of order processing in a medium-sized steel construction company in the field of special machine construction. Based on the product-process-resource modeling method and using the internationally standardized storage format AutomationML, the project will investigate how the automated step-by-step creation and execution of sales documents and production plans can be carried out on the basis of a detailed design. On the one hand, all important factors for a medium-sized company with regard to economic, qualitative, personnel-related and technological factors are to be taken into account and, on the other hand, simple applicability by management personnel is to be made possible.
In order to validate the automation options identified, a software prototype is to be developed with which the partner company can test the procedures and data models developed with regard to their practical applicability.
Funding body: FFG Austria via the Austrian Center for Digital Production (CDP)
Cooperations:
- [Vienna University of Technology
- Austrian Center for Digital Production (CDP)
- ATA Anlagentechnik Aschersleben GmbH & CO. KG
This text was translated with DeepL
Workflow automation in order processing in technical sales
Duration: 01.07.2023 to 31.03.2024
The aim of the project is to identify possibilities for the systematic automation of order processing in a medium-sized steel construction company in the field of special machine construction. Based on the product-process-resource modeling method and using the internationally standardized storage format AutomationML, the project will investigate how the automated step-by-step creation and execution of sales documents and production plans can be carried out on the basis of a detailed design. On the one hand, all important factors for a medium-sized company with regard to economic, qualitative, personnel-related and technological factors are to be taken into account and, on the other hand, simple applicability by management personnel is to be made possible.
To validate the automation options identified, a software prototype is to be developed with which the partner company can test the procedures and data models developed with regard to their practical applicability.
This text was translated with DeepL
Behavioral analysis of flexible components for handle-in-the-box systems
Duration: 01.06.2023 to 31.12.2023
The aim of the project is to research the behavior of flexible parts in robot-based grip-in-the-box (rGiK). RGiK applications for rigid components, especially metal parts, have been realized in research and are in the early stages of application in the automotive industry. They are based on the reliable detection of the position of the workpieces to be handled, which then enables precise gripping. The fixed shape of the component to be handled plays an important role here, enabling pattern matching for position detection.
Flexible components do not have these stability properties. Their position cannot be detected by simple pattern matching. The research project will evaluate how the detection and handling systems must be controlled in order to enable rGiK for flexible parts and where current hardware and software limitations exist that could motivate further research.
This text was translated with DeepL
Simulative analysis system for handle-in-the-box systems
Duration: 01.11.2022 to 31.12.2022
The aim of the project is the conception and prototypical implementation of a simulative analysis system for the evaluation of the reachability of a target point set for "reach into the box" applications in car body manufacturing. The aim is to answer the question: Can a robot reach a list of points without collision?
This text was translated with DeepL
2024
Book chapter
Objective method-based requirement gathering for digital data logistics processes in industrial projects
Hansch, Kevin; Große-Kreul, Alexander; Lüder, Arndt; Kuhlenkötter, Bernd
In: 2024 IEEE 29th International Conference on Emerging Technologies and Factory Automation (ETFA) / IEEE International Conference on Emerging Technologies and Factory Automation , 2024 - [Piscataway, NJ] : IEEE, insges. 4 S. [Konferenz: IEEE 29th International Conference on Emerging Technologies and Factory Automation, ETFA, Padova, Italy, 10-13 September 2024]
Development of PPR-based basic elements for methodical combination to generalist product twins in basic engineering for SME
Hansch, Kevin; Lüder, Arndt; Hoffmann, David
In: 2024 IEEE 29th International Conference on Emerging Technologies and Factory Automation (ETFA) / IEEE International Conference on Emerging Technologies and Factory Automation , 2024 - [Piscataway, NJ] : IEEE, insges. 8 S. [Konferenz: IEEE 29th International Conference on Emerging Technologies and Factory Automation, ETFA, Padova, Italy, 10-13 September 2024]
Peer-reviewed journal article
Evaluation methodology for selecting data exchange technologies for plant design processes
Große-Kreul, Alexander; Hansch, Kevin; Drees, Tobias; Lüder, Arndt; Kuhlenkötter, Bernd
In: Procedia CIRP / CIRP - The International Academy for Production Engineering - Amsterdam [u.a.] : Elsevier, Bd. 130 (2024), S. 1130-1136
Towards optimization methods for order data management - a case study of a medium-sized special purpose machinery manufacturer
Hansch, Kevin; Lüder, Arndt; Hoffmann, David
In: IFAC-PapersOnLine / Internationale Förderung für Automatische Lenkung - Frankfurt : Elsevier, Bd. 58 (2024), Heft 19, S. 121-126